Michigan ego training auto is causing a major shift in workplace safety this year. At Ford’s Rouge Plant in Detroit, a groundbreaking Ego-Awareness course has slashed oversight errors by 18 percent and cut near-miss accidents in half among 1,200 workers. Launched on May 2, 2025, by UAW Local 600 and plant management, this innovative program integrates mindfulness and emotional regulation into the daily grind of auto assembly. With plans for a wider rollout, this initiative could redefine safety standards across the industry.
A New Approach to Safety
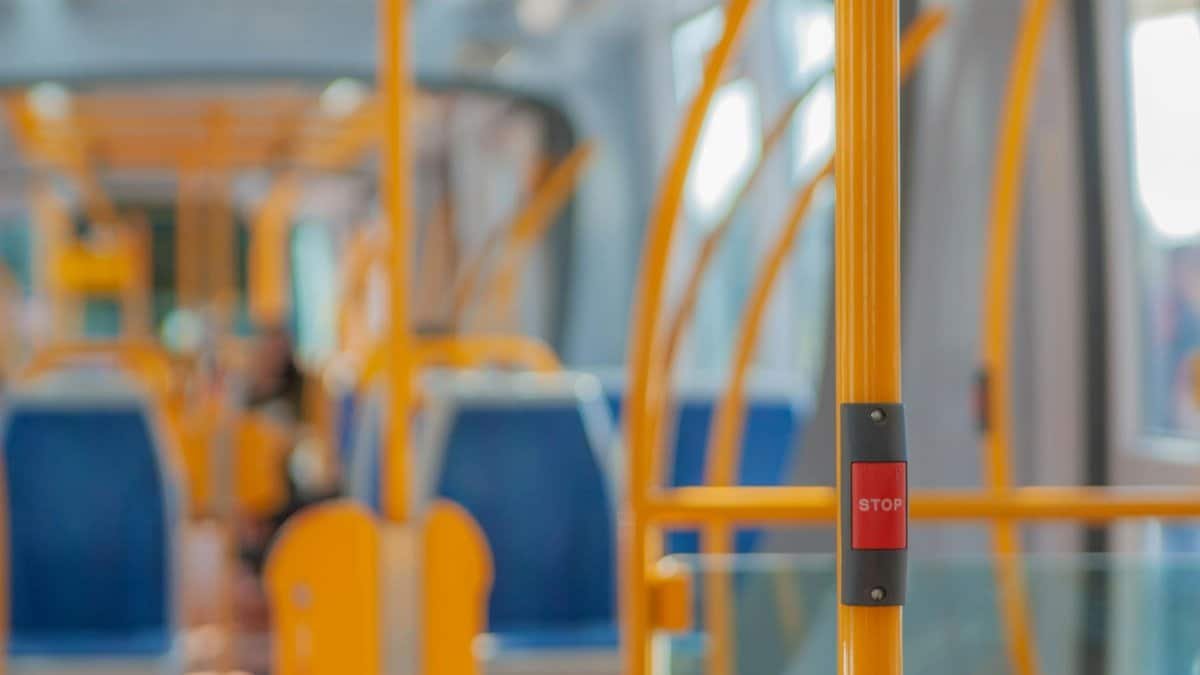
In an industry often defined by physical hazards, Ford’s Rouge Plant is tackling an overlooked factor: the human ego. The Ego-Awareness course, introduced in early May 2025, aims to help workers manage stress and interpersonal friction on the assembly line. Developed in collaboration with UAW Local 600, the program reflects a growing recognition that mental and emotional states play a critical role in workplace safety. By addressing these intangible risks, the plant is seeing tangible results.
Breaking Down the Four Modules
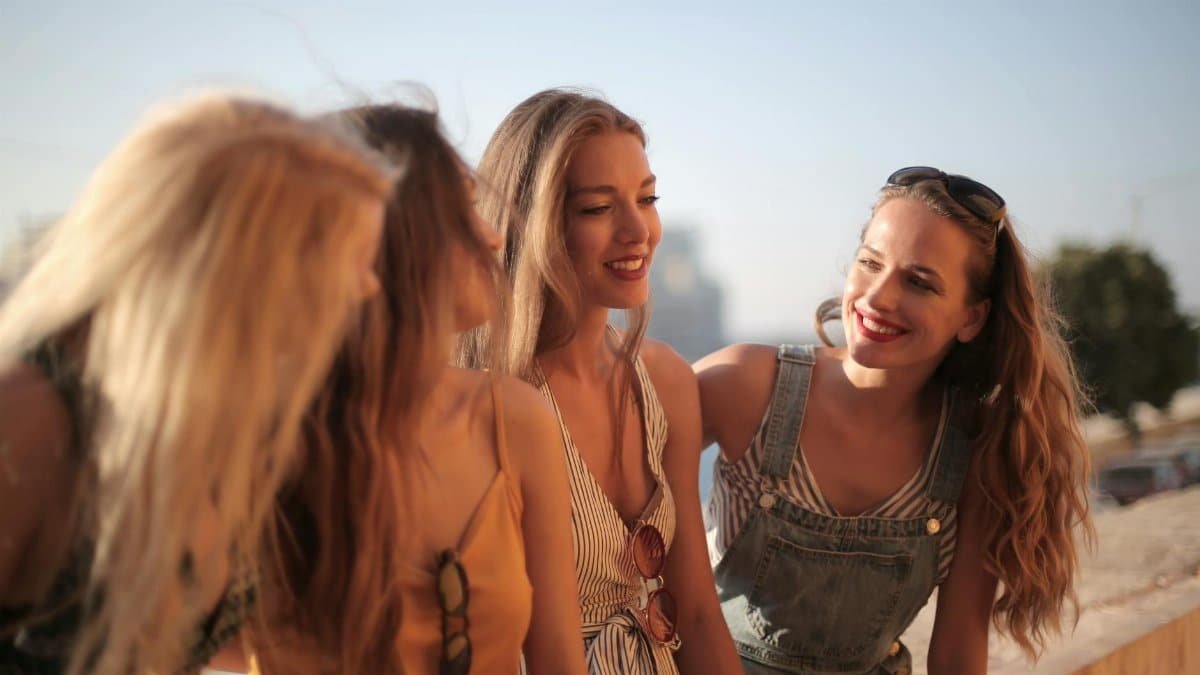
The training consists of four distinct modules, each designed for practical application during a worker’s shift. The first, breath resets, encourages employees to take a moment at the start of their shift to center themselves with controlled breathing. This simple act helps reduce initial stress and sets a focused tone for the day. The second module, buddy shadow check-ins, pairs workers to briefly assess each other’s mindset, fostering accountability and support.
Mindful Torque and Gratitude Practices

The third component, mindful torque application, teaches workers to approach repetitive tasks with intentional focus, reducing errors caused by distraction or frustration. Finally, the two-minute gratitude circle at shift end brings teams together to reflect on positive contributions, easing tensions that might otherwise spill over. These practices, though unconventional for an industrial setting, are proving their worth in day-to-day operations at the Rouge Plant.
Measurable Impact in Just 30 Days
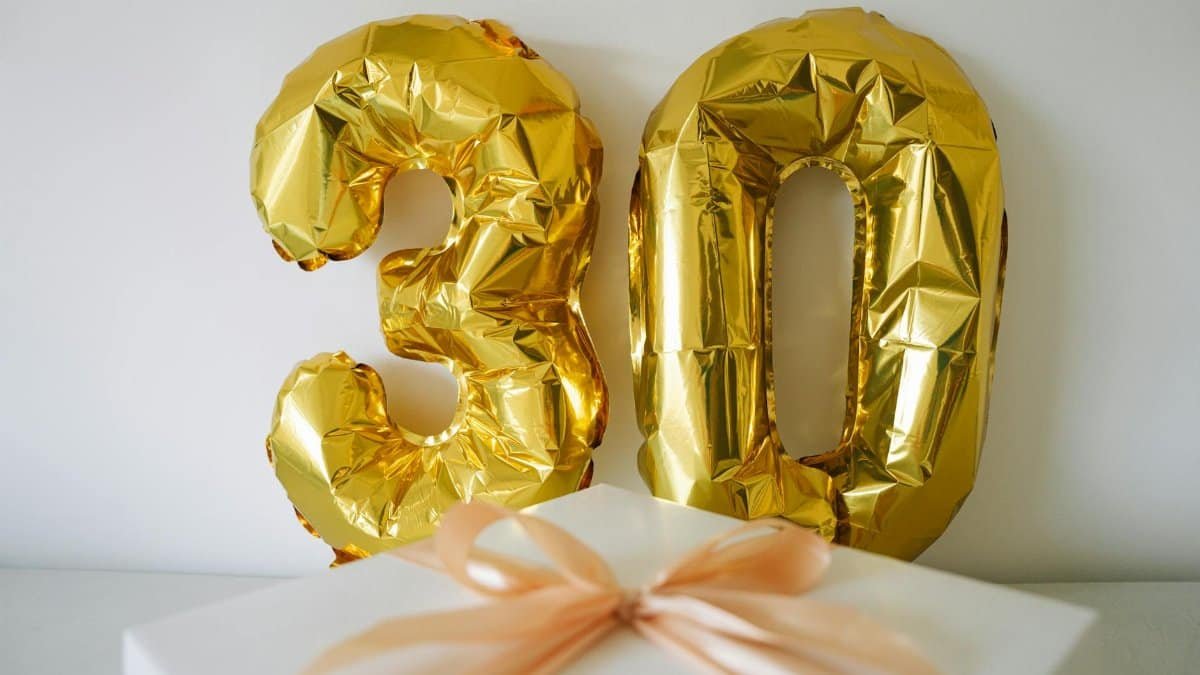
The numbers speak for themselves. Within 30 days of implementing the Ego-Awareness course, oversight errors among the 1,200 participating workers dropped by 18 percent. Near-miss accidents, which can signal potential for serious injury, fell from 12 to 6 in the same period. These early results suggest that addressing emotional and mental factors can directly improve physical safety outcomes in high-pressure environments like auto manufacturing.
Worker Response and Adaptation
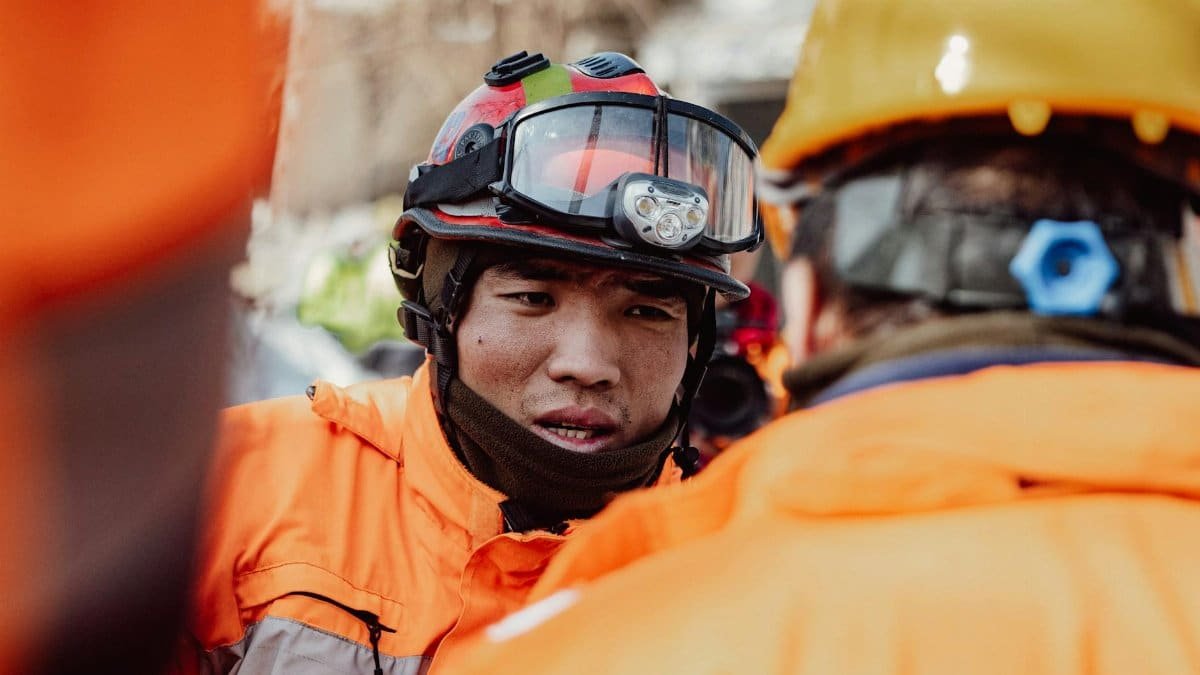
While the program introduces a cultural shift, initial feedback from Rouge Plant workers indicates growing acceptance. The structured modules fit seamlessly into existing routines, requiring minimal time while offering immediate benefits. For many, the buddy check-ins and gratitude circles have strengthened team dynamics, reducing conflicts that often lead to mistakes. As workers adapt to this new mindset, the plant is becoming a testing ground for a broader transformation.
Ford’s Plans for Expansion
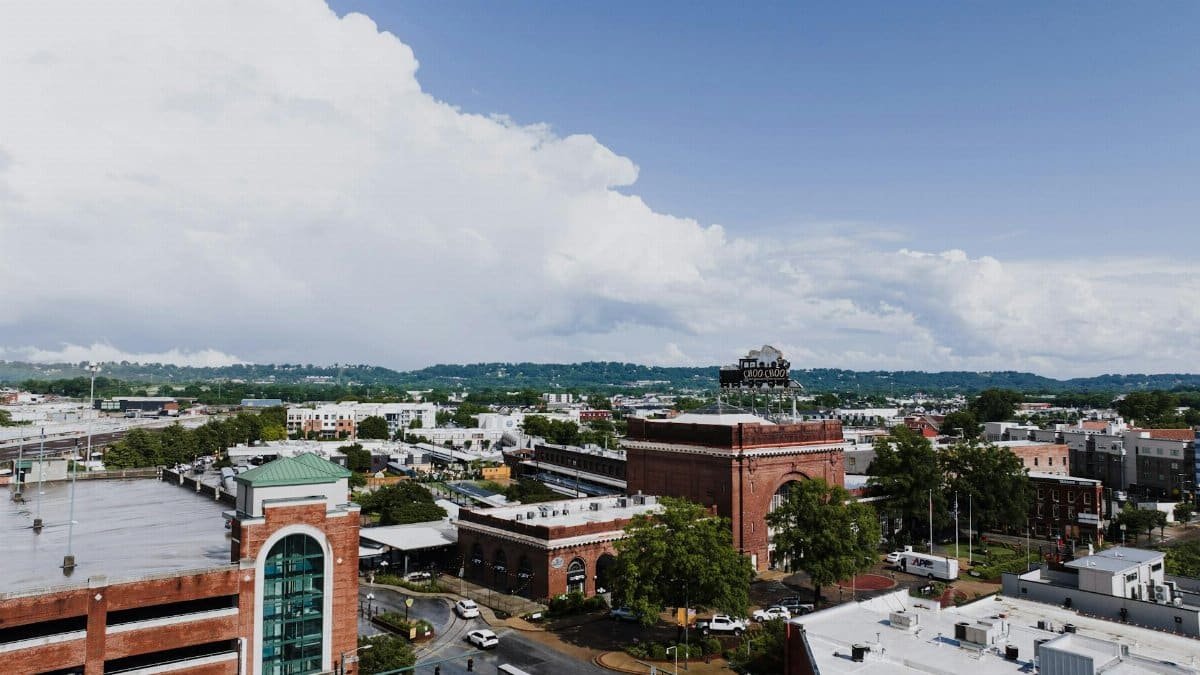
Ford HR Vice President Marcus Lee is already looking ahead. Impressed by the program’s early success, Lee has committed to a plant-wide rollout by the fourth quarter of 2025. This expansion will bring the Ego-Awareness course to thousands more workers at the Rouge Plant, potentially setting a precedent for other Ford facilities. Lee’s vision is clear: integrate emotional wellness into the core of industrial safety protocols.
National Implications and OSHA Involvement
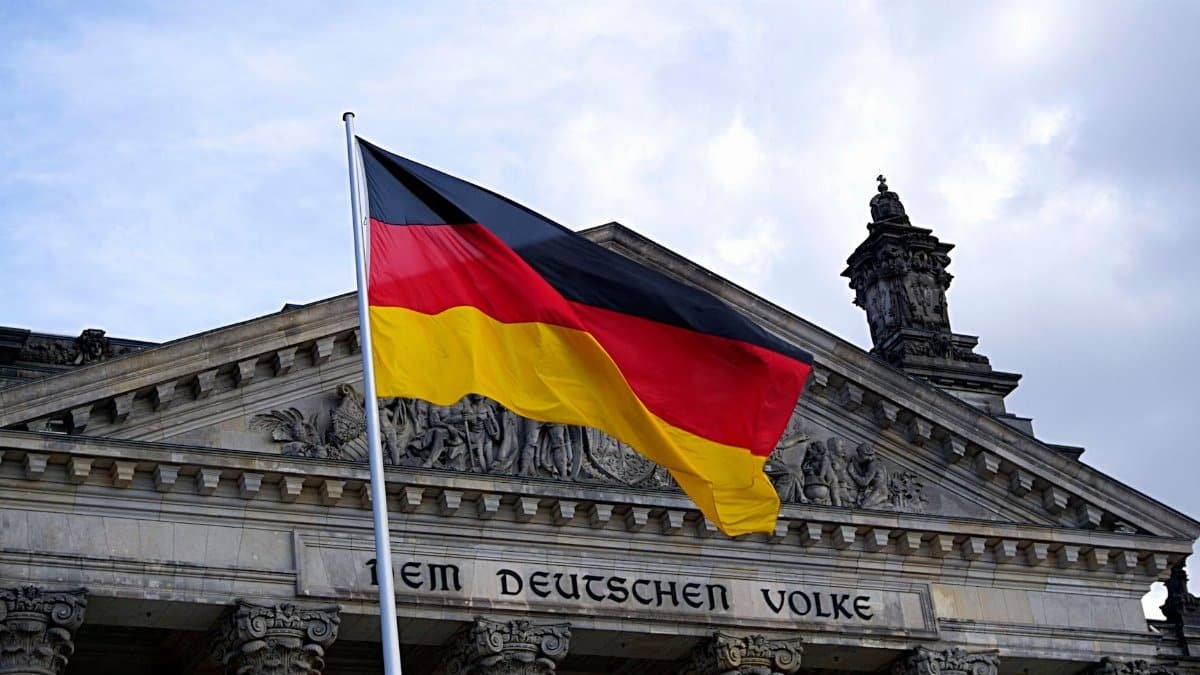
The impact of Michigan ego training auto may extend far beyond Detroit. Ford is sharing its data with the Occupational Safety and Health Administration (OSHA), hoping to inform national guidelines for workplace safety. If adopted, these practices could influence policies across industries, prioritizing mental and emotional health alongside traditional safety measures. For now, the collaboration with OSHA underscores the program’s credibility and potential for widespread change.
Context in U.S. Labor Trends
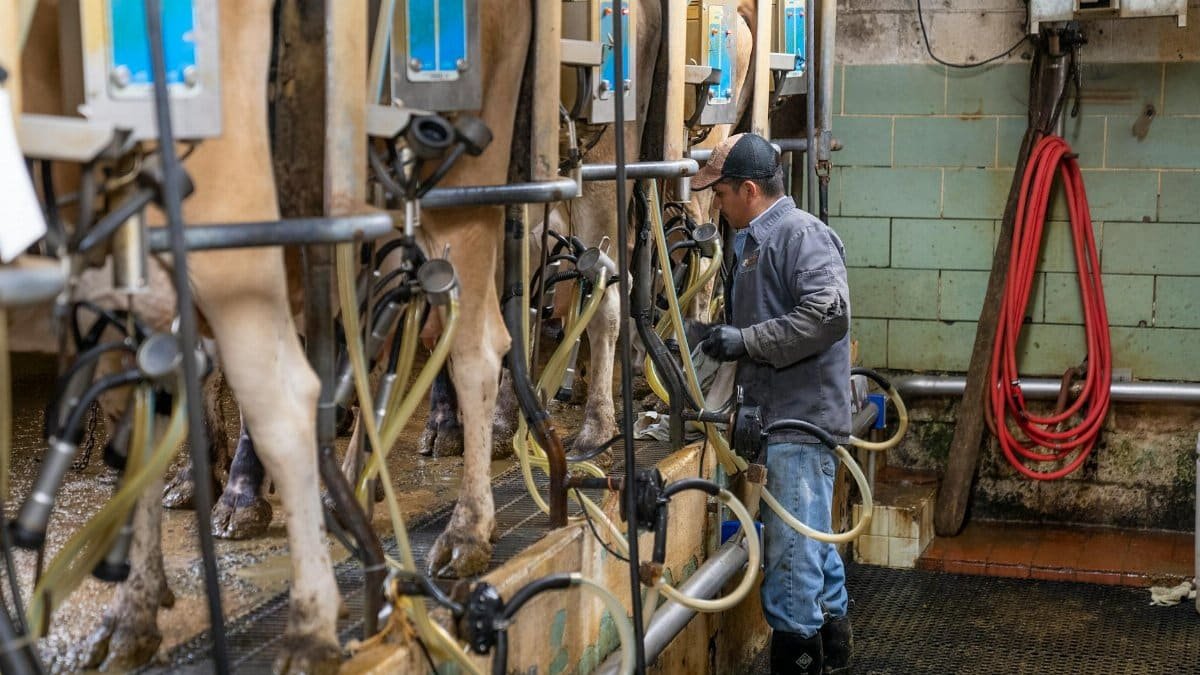
This initiative aligns with a broader push in 2025 for holistic workplace safety across the U.S. Labor unions and corporations alike are increasingly recognizing the link between mental well-being and productivity. Programs addressing stress and interpersonal dynamics are gaining traction, as evidenced by similar efforts in other sectors. For further reading on workplace safety trends, see resources from the Occupational Safety and Health Administration and insights on labor wellness from the Pew Research Center.
Challenges and Future Questions
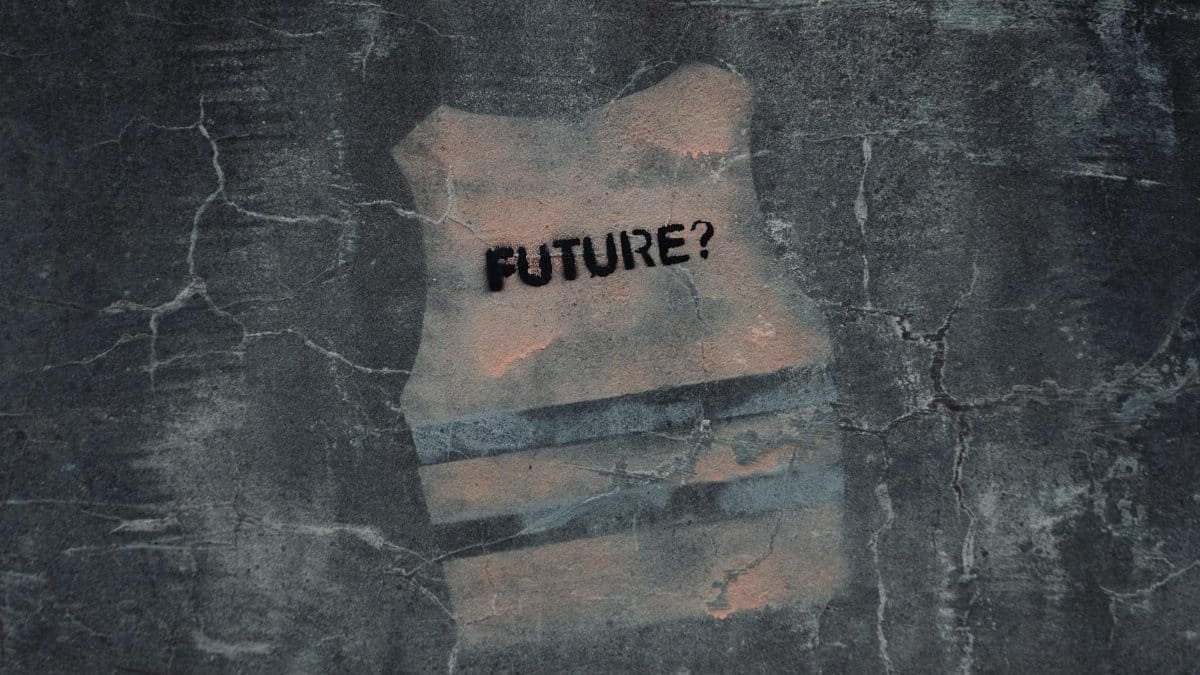
Despite its success, the Ego-Awareness course faces hurdles. Scaling the program to a larger workforce will require consistent training and buy-in from all levels of staff. Skepticism about “soft skills” in a hard-edged industry may also persist. Yet, as Michigan ego training auto gains momentum, it raises a critical question: can emotional awareness become as fundamental to safety as hardhats and steel-toed boots? The Rouge Plant’s experiment may soon provide the answer.